Tired of tied-up capital in the warehouse? Win back control of your stock
Stock management is one of the keys to a successful business
Manufacturers that fail to monitor stock effectively often find themselves dedicating valuable time and resources to additional stocktakes in an effort to regain control. Some replenish stock reactively, taking action only when something runs out, rather than making strategic decisions and purchasing materials based on planned requirements over time.
A company unaware of its stock levels faces greater challenges in planning effectively, leading to unnecessary extra work. However, the biggest issue arises when poor material planning affects delivery to customers– resulting in significant cost to the business.
Overstocking is another common pitfall. While maintaining adequate levels of commonly used materials is beneficial, the tendency to over-prepare can sometimes result in “hoarding”. This practice ties up capital that could be better utilized elsewhere.
Fortunately, help is at hand. Identifying trends and patterns can enable warehouse personnel to address issues and take control before things get out of hand. Here are four telltale signs your company’s stock management processes may need attention.
1. High volume of wastage
Inefficient sheet metal cutting processes can lead to excessive scrap or off-cuts, negatively impacting profitability. Effectively utilizing and recycling these materials is essential for controlling costs.
The solution:
- Implementing processes that minimize material wastage is critical. Effective cutting technologies, such as nesting, combined with recycling systems, are key tools for manufacturers.
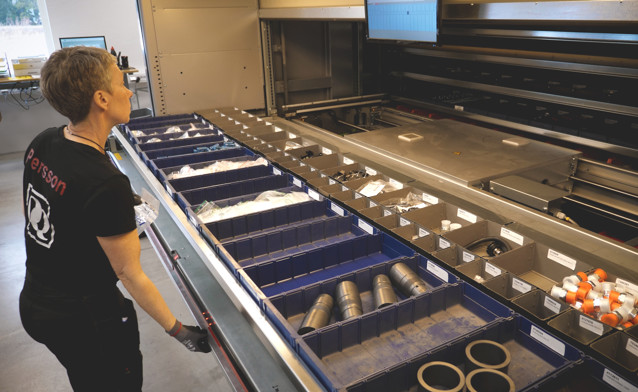
2. Difficulty tracking materials
Sheet metal comes in a wide variety of grades, thicknesses, and sizes, making stock management complex. Managing an array of metals (e.g., stainless steel, aluminum, copper) and ensuring the correct type is always available can be a significant challenge.
The solution:
- A fully integrated Enterprise Resource Planning (ERP) system like Monitor ERP helps sheet metal manufacturers track inventory in real time, manage re-ordering needs, and streamline operations.
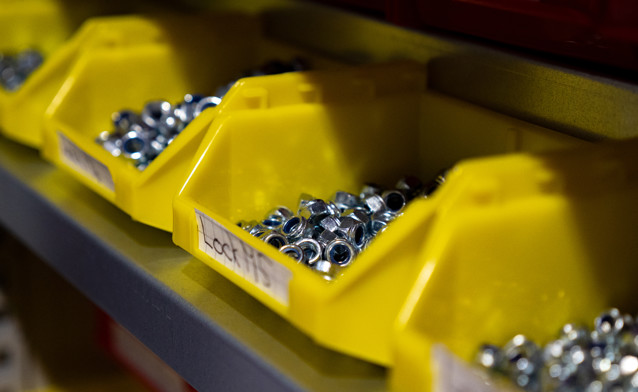
3. Warehouse disorganization and lack of space
A common complaint among warehouse staff is the inability to locate materials when needed. This is a sign of poor warehouse organization, leading to wasted time, missed sales opportunities, and inaccurate forecasting.
The solution:
- A warehouse management system – or WMS – helps companies manage daily warehouse operations, from receiving goods and materials to dispatching them. This tool streamlines every aspect of inventory management, improving efficiency and organization.
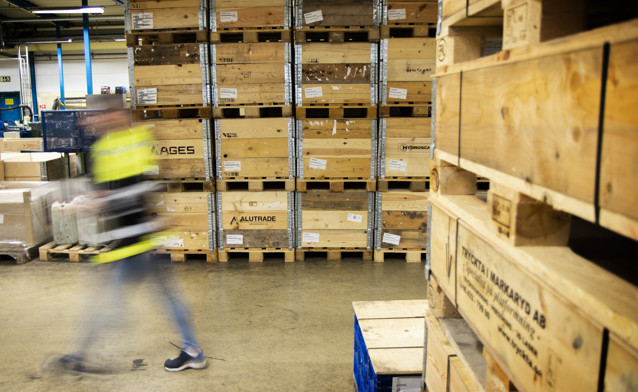
4. Holding way too much stock
Overstocking is a frequent issue in warehouses, where manufacturers hold excessive quantities of materials or components. This ties up valuable capital, hinders investment in other areas, and can lead to outdated stock that no longer meet standards.
The solution:
- Just-In-Time (JIT) Inventory minimizes storage costs by maintaining inventory levels as low as possible and ordering products only when required. JIT relies on strong supplier relationships, which enhance flexibility, reduce lead times, and enable quick replenishment during sudden demand spikes.
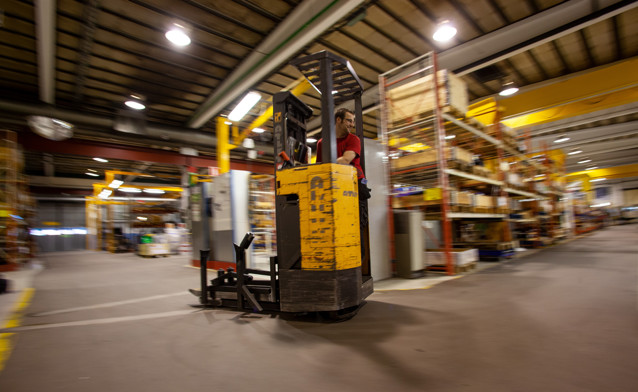
The science of stock management
The takeaway
Stock management for sheet metal manufacturers comes with many challenges. Holding excessive amounts of a particular material can be costly, while holding too little poses risks. Effectively managing waste, along with maintaining a lean and efficient warehouse, is critical. Proper coordination, structured inventory management, and strong supplier relationships are essential to fulfilling orders on time and staying competitive in today’s market.
In an increasingly digital world, sheet metal manufacturers must leverage the capabilities of enterprise resource planning (ERP) systems, along with strategies like Just-in-Time delivery, waste management, and nesting, to remain profitable and stay ahead of the competition.